Trong phòng sạch sản xuất vô trùng, vị trí lắp đặt FFU (Fan Filter Unit) đóng vai trò then chốt quyết định độ sạch và hiệu quả vận hành toàn hệ thống. Lắp sai vị trí không chỉ làm tăng nguy cơ nhiễm khuẩn, mà còn gây lãng phí năng lượng và chi phí bảo trì. Vậy đâu là nguyên tắc tối ưu hóa vị trí FFU để vừa đảm bảo lưu lượng khí chuẩn
Tóm tắt
Vậy đâu là nguyên tắc tối ưu hóa vị trí FFU để vừa đảm bảo lưu lượng khí chuẩn, vừa tiết kiệm chi phí? Cùng Thiết bị phòng sạch VCR tìm hiểu ngay những bí quyết bố trí FFU hiệu quả nhất cho phòng sạch sản xuất vô trùng trong bài viết dưới đây!
1. Mở đầu
Trong môi trường sản xuất vô trùng, chỉ cần một sai sót nhỏ trong thiết kế phòng sạch cũng có thể dẫn đến hậu quả nghiêm trọng như nhiễm chéo vi sinh, rớt kiểm định GMP hoặc thậm chí thu hồi sản phẩm trên diện rộng.
Một trong những yếu tố quyết định độ sạch và an toàn cho phòng sản xuất chính là bố trí đúng vị trí của Fan Filter Unit (FFU).
FFU không chỉ là thiết bị cấp khí sạch đơn thuần, mà còn đóng vai trò tạo nên luồng khí một chiều ổn định – tấm khiên bảo vệ sản phẩm trước mọi nguy cơ lây nhiễm. Tuy nhiên, rất nhiều nhà máy dược phẩm mắc phải lỗi bố trí FFU sai lệch, dẫn đến phân bố lưu lượng khí không đồng đều, dòng khí đảo ngược hoặc tích tụ hạt bụi ngay trên khu vực sản phẩm.
Vậy làm thế nào để tối ưu hóa vị trí FFU Fan Filter Unit trong phòng sạch sản xuất vô trùng, đảm bảo đúng tiêu chuẩn GMP-WHO, GMP-EU?
Trong bài viết này, chúng tôi sẽ chia sẻ những bí quyết thực chiến, giúp bạn thiết kế phòng sạch đạt cấp độ sạch lý tưởng ngay từ đầu, vận hành ổn định và vượt qua mọi kỳ audit khó tính nhất.
2. Tại sao tối ưu vị trí lắp đặt FFU lại quan trọng?
Trong phòng sạch sản xuất vô trùng, Fan Filter Unit (FFU) không chỉ đơn giản là thiết bị cấp khí sạch.
Nó đóng vai trò trái tim của hệ thống luồng khí một chiều, trực tiếp quyết định hiệu quả bảo vệ sản phẩm, nguyên liệu và môi trường sản xuất.
Việc bố trí FFU đúng vị trí mang lại những lợi ích không thể thay thế:
2.1. Đảm bảo cấp độ sạch theo tiêu chuẩn GMP
- Phân bố vị trí FFU hợp lý giúp duy trì độ sạch ISO Class 5 – Class 7 ổn định trong khu vực sản xuất.
- Đặc biệt với các khu vực aseptic (chiết rót, đóng gói vô trùng), việc phủ kín bề mặt hoạt động bằng dòng khí từ FFU là yêu cầu bắt buộc để đạt chuẩn GMP-WHO, GMP-EU.
2.2. Tạo luồng khí một chiều ổn định
- Khi FFU được lắp đúng cách, luồng khí đi từ trần xuống sàn theo hướng thẳng đứng, không tạo dòng xoáy, không khuấy đảo bụi bẩn.
- Đây là yếu tố then chốt giúp loại bỏ ngay lập tức các hạt vi sinh và hạt bụi phát sinh trong quá trình sản xuất.
2.3. Ngăn ngừa nhiễm chéo và tích tụ hạt bụi
- Nếu vị trí FFU không tối ưu, dòng khí sạch có thể va vào thiết bị, tường hoặc người vận hành rồi phản ngược lại – tạo ra dòng xoáy nhiễm chéo.
- Điều này vô cùng nguy hiểm trong môi trường sản xuất thuốc tiêm, vaccine, sinh phẩm yêu cầu vô trùng tuyệt đối.
2.4. Tiết kiệm chi phí vận hành và bảo trì
- Bố trí FFU hợp lý ngay từ đầu giúp giảm tải cho hệ thống HVAC tổng thể, từ đó tiết kiệm điện năng tiêu thụ và giảm chi phí bảo trì theo thời gian.
- Đồng thời, hệ thống dễ dàng điều chỉnh, giám sát hiệu quả thông qua BMS (Building Management System).
2.5. Đảm bảo thành công trong các kỳ audit GMP
- Các đoàn kiểm định WHO, EU, US-FDA cực kỳ chú trọng việc đo kiểm luồng khí, tốc độ dòng khí và phân bố áp suất.
- Một sơ suất nhỏ trong bố trí FFU cũng có thể khiến phòng sạch không đạt yêu cầu, gây trễ tiến độ và thiệt hại chi phí khắc phục rất lớn.
Xem thêm: Ưu điểm của FFU
3. Các yếu tố cần xem xét khi tối ưu vị trí Fan Filter Unit
Để bố trí FFU phòng sạch hiệu quả, không chỉ cần dựa vào cảm tính mà phải căn cứ trên các nguyên tắc kỹ thuật rõ ràng.
Dưới đây là những yếu tố quan trọng nhất cần cân nhắc để đảm bảo tối ưu vị trí FFU, đạt chuẩn luồng khí một chiều và cấp độ sạch theo tiêu chuẩn GMP.
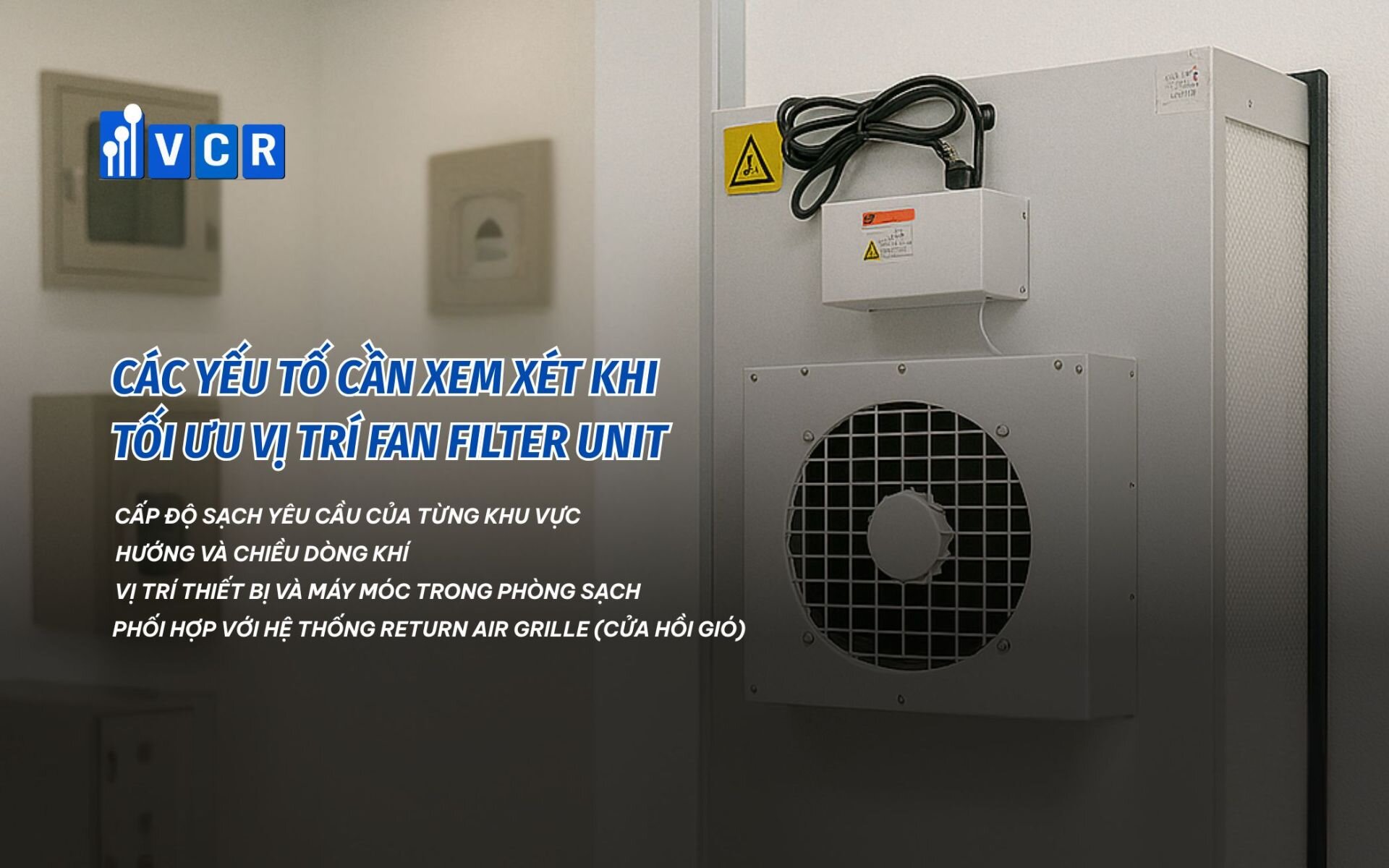
3.1. Cấp độ sạch yêu cầu của từng khu vực
- Mỗi khu vực trong phòng sạch vô trùng sẽ yêu cầu cấp độ sạch khác nhau, tương ứng với số lượng và mật độ lắp đặt FFU.
- ISO Class 5 (ví dụ: khu vực chiết rót vô trùng) cần mật độ FFU dày đặc hơn ISO Class 7 (khu vực hỗ trợ, chuẩn bị nguyên liệu).
- Cần tính toán chính xác số lượng FFU trên mỗi m² để đáp ứng được yêu cầu về tốc độ gió và tỷ lệ trao đổi khí (ACH).
3.2. Hướng và chiều dòng khí
- Luồng khí một chiều (laminar flow) phải được đảm bảo di chuyển thẳng đứng từ trên xuống, không tạo dòng xoáy.
- Tránh đặt FFU ngay sát vách tường, góc phòng, hoặc gần những chướng ngại vật lớn dễ gây xáo trộn dòng khí.
- Khi cần thiết, nên phối hợp FFU với các thiết bị dẫn khí hoặc điều hướng gió nhẹ để tối ưu đường đi của luồng khí sạch.
3.3. Vị trí thiết bị và máy móc trong phòng sạch
- Cần bố trí FFU trực tiếp phía trên khu vực sản phẩm nhạy cảm, như: bàn thao tác aseptic, máy chiết rót, đóng gói vô trùng.
- Tránh để FFU thổi khí vào các vật cản lớn gây dòng khí dội ngược, làm tăng nguy cơ nhiễm chéo hạt bụi, vi sinh.
- Ưu tiên thiết kế sao cho FFU hỗ trợ tối ưu hóa dòng khí bao phủ toàn bộ bề mặt sản xuất.
3.4. Phối hợp với hệ thống return air grille (cửa hồi gió)
- Một hệ thống lưu thông khí hiệu quả luôn yêu cầu sự kết hợp giữa FFU cấp khí sạch và cửa hồi gió hút khí bẩn.
- FFU nên bố trí ở trần phía trên khu vực aseptic, còn return grille nên bố trí ở tường thấp, đối diện hướng dòng khí đi xuống.
- Tạo thành luồng khí đơn hướng: khí sạch đẩy bụi bẩn và vi sinh ra khỏi khu vực aseptic một cách tự nhiên, hiệu quả.
4. Các mô hình bố trí FFU phổ biến cho phòng sạch vô trùng
Tùy theo mục tiêu sản xuất và cấp độ sạch yêu cầu, các nhà máy dược phẩm sẽ lựa chọn những mô hình bố trí Fan Filter Unit (FFU) khác nhau.
Dưới đây là 3 mô hình phổ biến nhất, được áp dụng rộng rãi trong thiết kế phòng sạch vô trùng.
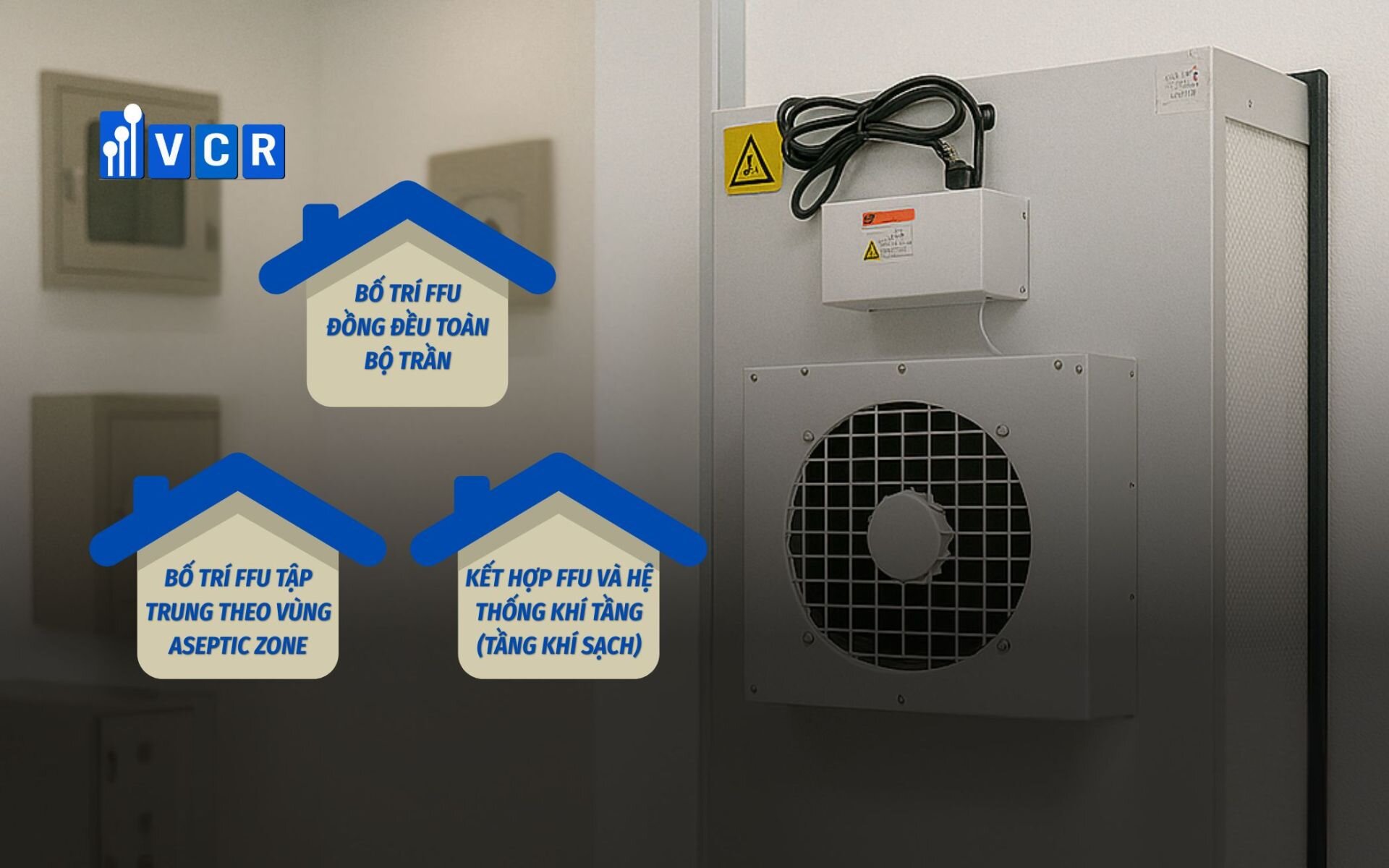
4.1. Bố trí FFU đồng đều toàn bộ trần
Mô tả:
- Các FFU được lắp đồng đều khắp toàn bộ diện tích trần phòng sạch, tạo ra luồng khí sạch đồng nhất, lưu lượng phân bố đều mọi khu vực.
Ưu điểm:
- Đảm bảo cấp độ sạch ổn định toàn phòng (ISO Class 5 hoặc cao hơn).
- Hạn chế tối đa vùng nhiễm bẩn hoặc dòng khí chết.
Ứng dụng:
- Phù hợp cho các khu vực sản xuất aseptic nhạy cảm như chiết rót thuốc tiêm, sản xuất vaccine, sinh phẩm.
4.2. Bố trí FFU tập trung theo vùng aseptic zone
Mô tả:
- FFU được lắp tập trung nhiều ở khu vực aseptic zone (nơi có nguy cơ cao như chiết rót, đóng gói vô trùng), còn các khu vực phụ trợ xung quanh sẽ lắp ít hoặc không cần FFU.
Ưu điểm:
- Tối ưu chi phí đầu tư FFU.
- Tập trung bảo vệ sản phẩm tại các vị trí nhạy cảm nhất.
Ứng dụng:
- Các dây chuyền sản xuất dược phẩm cần phân chia cấp độ sạch rõ ràng (ví dụ ISO 5 tại aseptic zone, ISO 7 tại khu hỗ trợ).
4.3. Kết hợp FFU và hệ thống khí tầng (tầng khí sạch)
Mô tả:
- Sử dụng FFU kết hợp với thiết kế khí tầng (air showers hoặc laminar flow systems) để dẫn luồng khí sạch xuống từng tầng, kiểm soát dòng khí tiếp xúc với sản phẩm và nhân viên.
Ưu điểm:
- Tăng cường bảo vệ từng bước trong quy trình sản xuất.
- Phù hợp với phòng sạch có nhiều máy móc cồng kềnh hoặc dây chuyền sản xuất phức tạp.
Ứng dụng:
- Nhà máy dược phẩm sản xuất theo dây chuyền tự động hóa, sản phẩm đòi hỏi kiểm soát vô trùng tuyệt đối.
5. 5 lưu ý vàng khi bố trí FFU cho nhà máy dược phẩm
Một hệ thống Fan Filter Unit (FFU) hoạt động hiệu quả không chỉ phụ thuộc vào chất lượng thiết bị, mà còn đòi hỏi kỹ thuật bố trí chuẩn chỉnh ngay từ đầu.
Dưới đây là 5 lưu ý quan trọng mà bất kỳ dự án phòng sạch sản xuất vô trùng nào cũng cần nắm chắc.
5.1. Không để khoảng cách giữa các FFU quá lớn
- Nguyên tắc: Khoảng cách tối đa giữa các FFU không nên vượt quá 500mm – 600mm (tùy cấp độ sạch yêu cầu).
- Vì sao? Nếu khoảng trống quá lớn, luồng khí sạch sẽ không bao phủ đồng đều, dễ tạo ra vùng dòng xoáy hoặc điểm chết chứa hạt bụi và vi sinh.
5.2. Ưu tiên lắp FFU phía trên khu vực sản phẩm nhạy cảm
- Khu vực nào cần ưu tiên? Các vị trí như bàn chiết rót, máy đóng gói vô trùng, khu vực tiếp xúc trực tiếp với sản phẩm.
- Mục tiêu: Đảm bảo sản phẩm luôn nằm trong vùng luồng khí sạch nhất, hạn chế tối đa nguy cơ nhiễm tạp chất.
5.3. Luồng khí FFU phải phủ kín bề mặt hoạt động
- Yêu cầu: Luồng khí từ FFU phải trải đều, phủ kín toàn bộ vùng thao tác và thiết bị.
- Cảnh báo: Nếu dòng khí không phủ đều, bụi và vi sinh có thể tồn đọng tại các góc khuất, gây nguy cơ nhiễm chéo rất cao.
5.4. Đảm bảo khoảng cách hợp lý giữa FFU và thiết bị
- Khoảng cách lý tưởng: FFU nên cách bề mặt thiết bị ít nhất từ 800mm – 1200mm để luồng khí đạt độ ổn định trước khi tiếp xúc.
- Tại sao? Nếu khoảng cách quá gần, luồng khí chưa ổn định dễ tạo dòng rối; quá xa thì khó kiểm soát vùng sạch.
5.5. Kiểm tra mô phỏng CFD (Computational Fluid Dynamics) trước khi thi công
- Tầm quan trọng: Mô phỏng CFD cho phép dự đoán luồng khí, phát hiện sớm các vùng dòng xoáy, vùng chết, trước khi thi công thực tế.
- Lợi ích: Giúp tối ưu thiết kế FFU, tiết kiệm chi phí chỉnh sửa sau này và đảm bảo đạt cấp độ sạch ngay lần nghiệm thu đầu tiên.
6. Kết luận
Trong sản xuất vô trùng, nơi mà chỉ một hạt bụi cũng có thể gây ra hậu quả khôn lường, việc tối ưu vị trí lắp đặt Fan Filter Unit (FFU) không chỉ là một yêu cầu kỹ thuật, mà còn là nền tảng cốt lõi đảm bảo an toàn và chất lượng sản phẩm.
Một hệ thống FFU bố trí hợp lý sẽ:
- Duy trì cấp độ sạch ổn định theo tiêu chuẩn ISO Class 5 – 7.
- Tạo ra luồng khí một chiều chuẩn mực, hạn chế dòng xoáy và nhiễm chéo.
- Bảo vệ sản phẩm vô trùng trong suốt quá trình sản xuất.
- Giúp nhà máy tiết kiệm chi phí vận hành và tăng khả năng vượt qua các kỳ audit GMP khắt khe.
Nếu bạn đang thiết kế, thi công hoặc nâng cấp phòng sạch sản xuất vô trùng, đừng bỏ qua công đoạn tối ưu vị trí Fan Filter Unit ngay từ giai đoạn đầu.
Một bản thiết kế chuẩn mực hôm nay sẽ là bảo hiểm an toàn cho vận hành ổn định suốt nhiều năm sau
Bạn đang cần tư vấn giải pháp tối ưu FFU cho nhà máy dược phẩm?
Hãy liên hệ ngay với chúng tôi để nhận tư vấn kỹ thuật miễn phí từ các chuyên gia phòng sạch hàng đầu!
Hieu VCR