Fan Filter Units (FFUs) play a crucial role in maintaining critical air quality standards within controlled environments like semiconductor, electronics, and biological cleanrooms. Their unique advantages and cost-effectiveness make them a popular choice, but successful installation hinges on meticulous adherence to specific conditions.
This expert guide, delving deeper into established industry practices, outlines the key factors to ensure a safe and successful FFU implementation.
Pre-Installation Cleanliness
1. Impeccable Cleanroom Environment: Prior to HEPA filter installation, the cleanroom must undergo a thorough cleaning regimen. Any internal particulate contamination, especially on the suspended ceiling where the FFU will reside, needs to be meticulously removed through wiping and cleaning procedures.
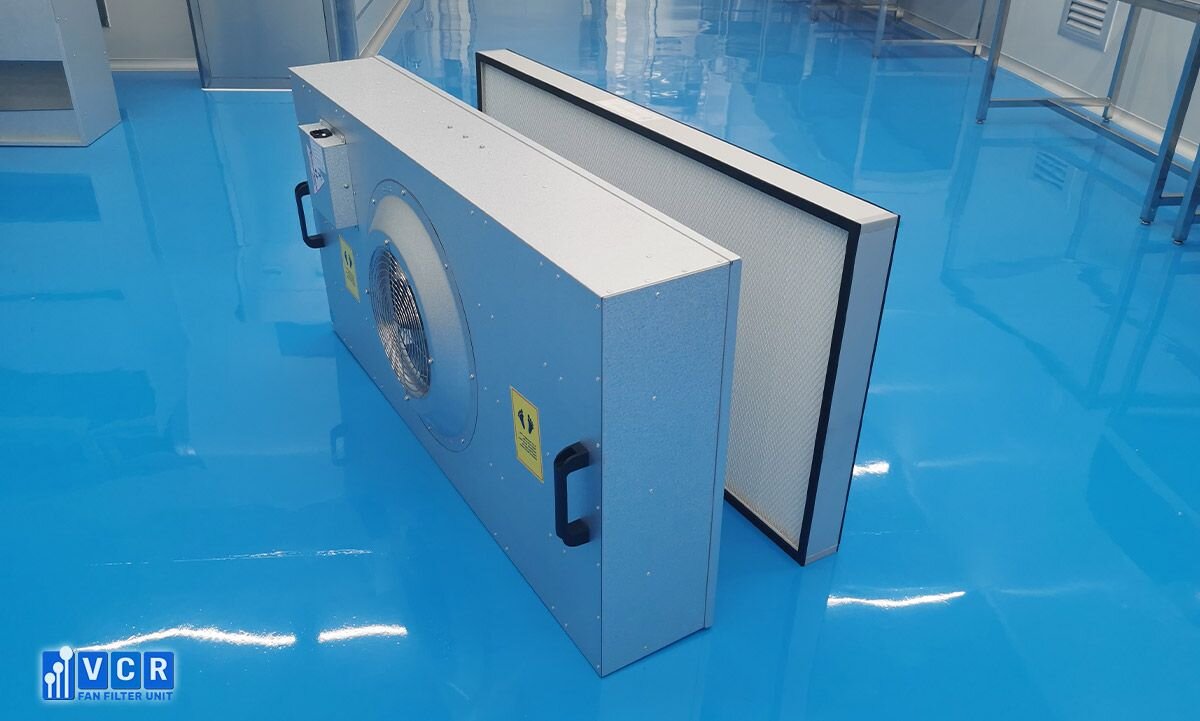
2. Airtight Integrity: Absolute airtightness is essential during installation. Once the FFU is in place and operational, a continuous trial run exceeding 12 hours should be conducted to verify airtightness before proceeding with HEPA filter installation.
See more: Fan Filter Unit Safety in Cleanroom
Maintaining a Cleanliness-First Approach
3. Particulate Control: Throughout the installation process, stringent measures must be taken to minimize airborne particles within the cleanroom. This includes implementing dust control methods and minimizing activity that could generate particulates.
4. Protective Attire: Installation personnel must wear designated cleanroom garments and gloves to prevent personal contamination of the FFU housing and filter.
5. Environmental Suitability: The installation environment should be free of dust, oil, excessive humidity, and corrosive liquids like water. These elements can negatively impact the long-term performance and effectiveness of the HEPA filter.
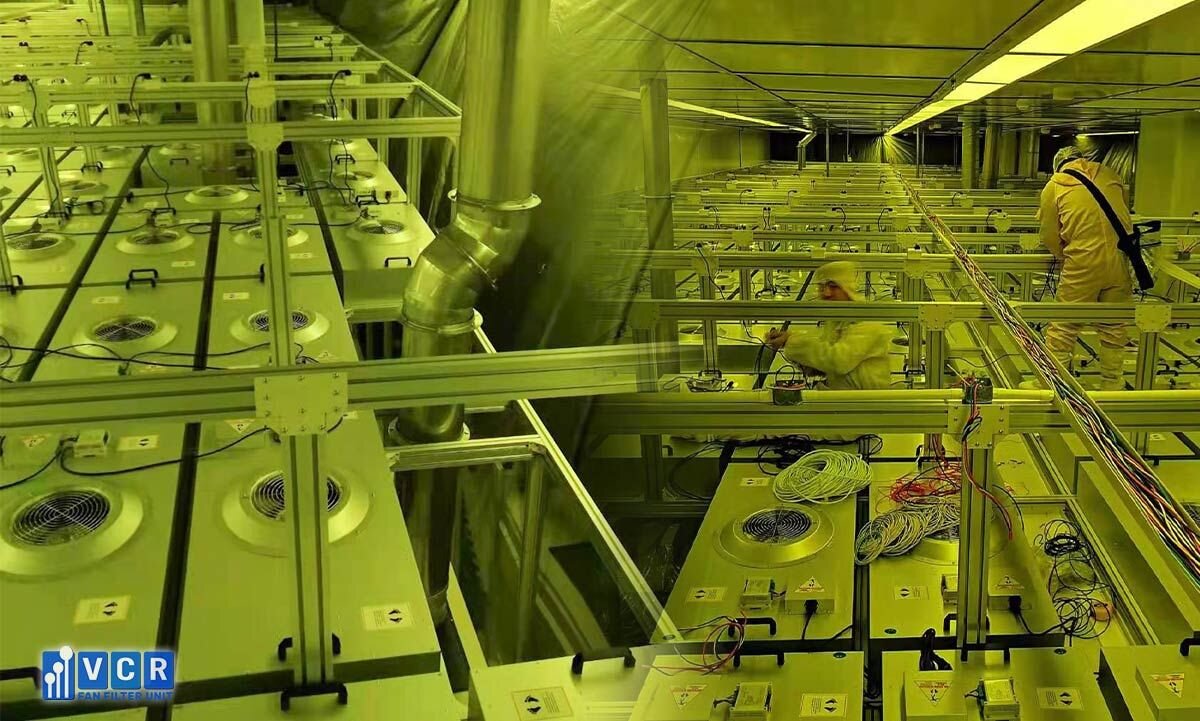
See more: Optimizing FFU Energy Efficiency
Additional Considerations
6. Installation Team Size: Limiting the number of installation personnel to a recommended maximum of six people helps minimize potential sources of contamination and streamlines the process.
Beyond the Basics:
While these conditions provide a robust foundation, remember that successful FFU installation often requires additional factors to be considered:
- Manufacturer-Specific Instructions: Always adhere to the specific guidelines and recommendations provided by the FFU manufacturer.
- Local Regulations and Standards: Ensure compliance with all relevant regional and industry-specific regulations and standards governing cleanroom operations and FFU installations.
- Qualified Personnel: Involve personnel with the necessary training and experience in cleanroom protocols and FFU handling to ensure proper execution.
- Ongoing Maintenance: Establish a comprehensive maintenance plan for regular filter replacements, performance checks, and cleaning to maintain optimal FFU functionality and air quality.
By carefully considering these expert recommendations and tailoring them to your specific cleanroom application, you can create a safe and efficient environment for FFU installation, ultimately ensuring optimal air quality and performance within your controlled space.